THE SUNILA FACTORY
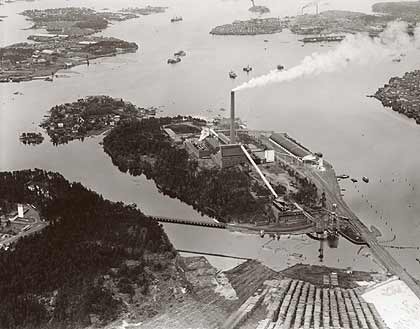
Photo: Finnish Armed Forces / Air Force.
The Sunila sulphate pulp mill was founded in order to produce unbleached kraft pulp as a
raw material for the five companies owning it - A. Ahlström, Enso-Gutzeit,
Yhtyneet Paperitehtaat [United Paper Mills], Kymi and Tampella - as well as for export.
The timber that was to be refined in the mill was transported via waterways and railway.
|
FROM TIMBER TO PULP
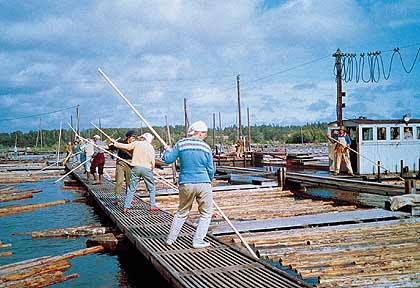
Photo: The Provincial museum of Kymenlaakso (PMK) / Trond Hedström 1963.
The timber was floated along the River Kymi in 15-ton bundles and then lifted with a cable crane into the wood yard to be stored, or was transferred with another type of crane directly to the de-barking plant, where the wood was cut and then transferred to debarking drums where it was turned into screened wood chips and then moved via silos into boilers. In the boiling agent the lignin dissolved from the wood leaving the solid matter, the cellulose fibre. The fibre mass was then pushed into washing vats. The washed cellulose fibre went via different sieves to a precipitator and from there to a pan grinder and finally to drying machines. With the first so-called Kamyr continuous digester the cellulose fibre was compressed together when wet, which reduced the water content to 50%, while the ready cellulose fibre coming from the fan drying machine only contained 10% water. The material was then cut into sheets which were pressed into 200 kg bales and taken to the stores and from there onwards to paper mills.
The boiling agent separated from the cellulose was recycled through an evaporation plant and the remaining lye was dried. The dried lye and the condensed lignin were burned in a furnace and the heat energy produced from it was recovered. When the separated chemicals were mixed in water it produced a sodium hydroxide solution. This was caustisized with lime, clarified and thus attaining a usable boiling agent. The boiling agent continued its unending cycle within the factory and losses were replaced with Glauber's salt, but the timber was taken as pulp bales out into the world via railway or onto ships in the factory's own harbour.
The production of chemical pulp follows similar principles today. Today, however, the factory is automated, all parts of the process have been completely renewed, the pulp is bleached and the waste water is biologically purified. There have also been air pollution protection stipulations to take into account.
|
THE STORY OF THE FACTORY
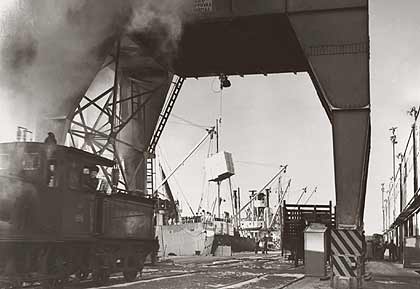
Photo: The Provincial museum of Kymenlaakso (PMK)
The beginning of factory operations was difficult: the demand for pulp was small and production had to be limited. During the Winter War the factory operations were mostly suspended and a large part of the workforce was in the front-line troops or otherwise engaged in the service of the Finnish defence forces. During the war years Sunila was run to a significant extent by women. As much as 65% of the staff operating the machines were women - under normal circumstances they made up 10% of the total workforce.
When the war ended the pulp market picked up. High inflation as well as difficulties in acquiring timber, coal and lime, however, slowed down the development of operations. In 1951 the factory reached its original annual production target of 80,000 tons and that same year the first extension project was initiated, after the completion of which, three years later, annual production increased to 120,000 tons. The next stage of expansion in 1958-1960 raised the annual production to over 200,000 tons.
The large-scale projects of the 1960s included the renewal and extension of the power plant and the construction of a new turbine and water purification plant. Production records again rose with the extension of the semi-bleaching plant. The new state-of-the-art full-bleaching plant started operating in 1970, and this large investment was followed by the construction of a large wood-handling plant. Like in many other fields, automation and information technology took over also in the pulp processing industry, and environmental issues began to become more pronounced also in investments. From 1978 onwards the effluent from the process was led to a new mechanical purification plant, and the biological activated sludge plant began operating in 1995. Today the emissions from Sunila are at the same levels as in other modern factories.
|
THE FUTURE OF THE PRODUCTION
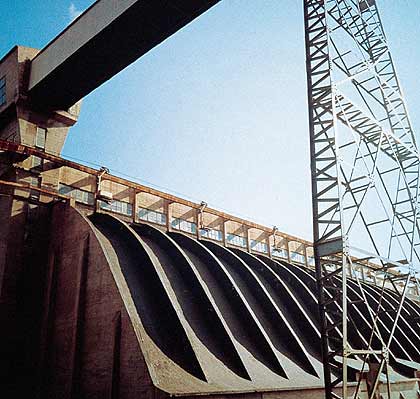
Photo: The Provincial museum of Kymenlaakso (PMK) / Trond Hedström 1963.
The annual production capacity of the Sunila company in 2003 is 350,000 tons, for which 2 million cubic metres of spruce and pine is needed. Over 50% of the wood and chips arrives to the factory by road, 15% by rail and 30% by sea (mainly from the Baltic States) via the factory's own harbour. The ready pulp is delivered mainly by road to clients in Finland and a part is shipped abroad.
In 2002 the factory, owned by the Myllykoski Paper company and the Stora Enso company, had a permanent workforce of 300.
The factory lives in its own time, and time leaves its mark on the appearance of the factory. Original working methods required facilities of a specific size, into which, however, it is not possible to place new equipment.Large factory halls have been abandoned and the newest extensions have been built outside the red brick envelope of the original factory building, and new massive 35-metre-tall silos, built for storing wood chips, have been located even further away.
|
» PDF (6,3Mb)
- Sirkka Soukka
|
|

|
|