"They have control rooms where they follow the process on monitoring gauges so one doesn't have to go and look every now and then to see how the pumps work: but before it was done by rule of thumb, so that when they did the boiling they could put the valve like that, and when the next boiler came then they turned it in a different position, because each shift had their own style… and when the pulp was washed in such a washing vat they looked into it and hosed it and let water in in different ways, whereas nowadays everything goes through a filter of course, they're not touched for weeks, they progress…"
This was how a retired Sunila employee, recalled, in 2003, the changes which happened in the factory during his working life from 1956 to 1983.
Usko Haapanen recounts: "In February-March there were 14 of us in Kaukopää, each studying a particular task. I studied the management of evaporation… for five weeks. We were very keen. By studying and trying ourselves we learned what the task demanded in practice. Typically you usually did not tell the next bloke of the nifty tricks we had discovered ourselves. We learned the basics in Kaukopää and the rest at home in Sunila."
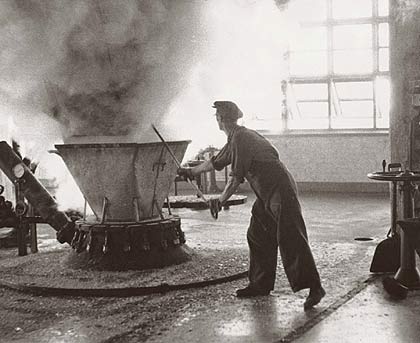
Photo: The Provincial museum of Kymenlaakso (PMK)
|
"WE DID OURSELVES WHAT WE COULD"
Pulp making continued as an essentially hand-made process until the 1960s. Once the renewal of the working methods began it then reached to every aspect of the production, but could most clearly be seen in the beginning and end stages of the process. In unloading the timber different machinery replaced people and pulp hooks, and the moving of the pulp bales was carried out entirely with fork-lift trucks.
Since the 1970s automatization and computerization have entailed the replacement of hundreds of workers. In the present pulp-making process, the workforce is mainly needed to observe and follow the process with monitoring devices, inspecting the quality of the product and doing any necessary maintenance work of the processing machinery.
Many of the stages of the work process that no longer exist were difficult and heavy. Inspecting the ready 200-kg pulp bales, weighing and pushing the material onto the press was considered "delicate work and often even women's work". In the same way, transporting the bales from the harbour warehouses to the ships required both skill and perseverance, on top of being heavy work.
There was a foundry in the machine repair shop, but this was closed down in the 1960s. Even some pump models were made in the foundry, in moulds made by the factory's own joiner. All in all, self-reliance and self-initiative was seen as part of the job during the era of the patriarch Kanto; his principle was that they themselves should try and make everything that it was possible to make.
The few hundred men in the repair workshop - lathe workers, milling operators, filers, planing-machine operators, fitters, plumbers and sheet metal workers - repaired and made new parts when needed, even improvising as necessary. As the technology used in the factory at the time was simpler and more straightforward than it was later to become, the electricians developed their own gadgets and equipment, apparatuses for the machines that transported pulp bales and other things.
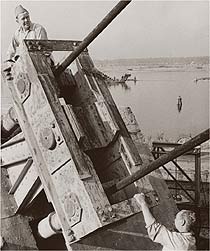
Photo: The Provincial museum of Kymenlaakso (PMK), the Matti Kanto Collection.
|
» PDF (1,7Mb)
- Sirkka Soukka
|
|

|
|